Infographic
Story of the collapse
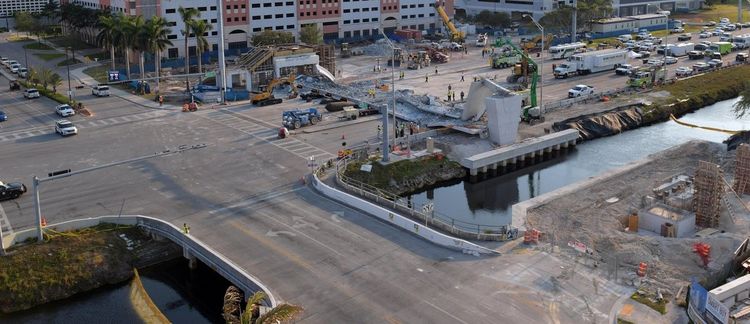
Analysis
Incident details
The bridge at FIU was designed to let pedestrians and cyclists safely cross the busy highway separating the main campus in western Miami from a popular student housing area in the neighbouring city of Sweetwater. It was also meant to be a landmark structure.
The design specified two precast concrete spans: a 53m main span to cross the highway – South-West Eighth Street – 15m west of its junction with South-West 109th Avenue; and a 30m back span to cross the Tamiami Canal, which runs parallel to the highway.
An architectural embellishment in the form of a 33m-tall mast and 10 steel pipe stays replicated the aesthetics of a cable-stayed bridge but would play no part in supporting these spans. The concrete bridge design comprised a 9.75m-wide deck and 4.88m-wide canopy, sitting 4.57m above the deck. Together these formed the upper and lower chord members of a central longitudinal truss.
This single truss was made up of vertical and diagonal members of varying lengths set at non-standard angles, with the diagonals aligning to the stays above. The main span's 12 truss members were 533mm wide (transversely) and ranged in depth (longitudinally) from 610mm to 914mm.
The design meant some main span truss members were permanently post-tensioned via internal post-tensioning rods, while others were not designed to be post-tensioned. Diagonal members 2 and 11 were temporarily post-tensioned, again using post-tensioning rods, to address construction requirements.
Only the main span had been constructed at the time of the collapse.
A most uncommon design
Truss structures carry both tensile and compressive forces, so they’re usually made of steel, rather than steel-reinforced concrete. They’re also usually connected by cross-members to create a degree of load-path redundancy – that is, the ability to carry loads after damage to, or the failure of, one or more members.
Temporary and permanent post-tensioning in the concrete truss should have ensured that all members could resist the load effects within them in both temporary and permanent conditions. Reinforced concrete truss structures are rare – and it’s thought that there is no precedent for single-truss (non-redundant) bridges.
State authority transport projects in the US are usually low-risk undertakings, but this one was not. Because it had no professional engineers on its payroll, FIU had to rely on external consultants and contractors to deliver the project. The intricate nature of the design should have prompted the authority concerned – the Florida Department of Transportation (FDOT) – to have more of an oversight or even reject the design for being too complex. Current US standards fail to address redundancy in reinforced concrete trusses, particularly for uncommon bridge structures.
Early misunderstandings
Initially, the designer engaged by FIU mistakenly assumed that its in-house team could verify its design. It needed to be informed that an independent third party had to do this under the FDOT’s standards. These also stated that only a reviewer that had been qualified by the FDOT to analyse a structure of this nature could perform the task.
Initially, the designer engaged by the university mistakenly assumed that its in-house team could verify the design. It needed to be informed that an independent third party had to do this
One bidder for the independent review work quoted $110,000 to verify the design – a job that included checking truss-member connections (nodes). Other bidders submitted much lower quotations. So, to win the contract, this reviewer slashed its quote to $61,000 (the sum available in the budget for the work) and stated that it could complete the process three weeks sooner than it had originally estimated.
An important omission
The requirement to roughen the surface of hardened concrete before fresh concrete was poured on to it (to prevent a discontinuity at the ends of diagonal members) was not included in the drawings for node 11/12. This factor, combined with the numerous voids created for service pipes embedded in the concrete, reduced the structure’s strength.
To minimise disruption to traffic, the construction involved casting the main deck, truss and canopy on open ground beside the highway on a temporary structure featuring several props. Once the casting was complete, the props were removed sequentially until the bridge was held up by two end supports. Cracks appeared at this stage, yet the engineer responsible onsite saw no problem in that.
Cracks worsened at node 11/12, yet nothing was done to investigate the cause, prop up the structure or even close the road
The design required that rods in the bridge’s end diagonal members (2 and 11) be tensioned before it was transported to its final position over the highway and that this tensioning be reversed thereafter. During that process, cracks worsened at node 11/12, yet nothing was done to investigate the cause, prop up the structure or even close the road.
On the day of the incident, member 11 was re-tensioned to remedy the cracking – in the absence of both a peer review and a post-tensioning inspection. The re-tensioning process increased demand in the 11/12 node, leading to its failure. This caused the bridge to collapse on to the busy highway, killing one construction worker and five vehicle occupants. Ten others were injured, six seriously.
The chief causes of the failure and the lessons learnt can be grouped into the following categories and are discussed in detail in the below chapters:
- Cause 1: A lack of understanding of the bridge’s uncommon design
- Cause 2: Structural design errors
- Cause 3: The design reviewer’s failure to detect those errors
- Cause 4: Inadequate responses when cracks appeared in the structure
- Cause 5: The poor judgement of the engineer of record
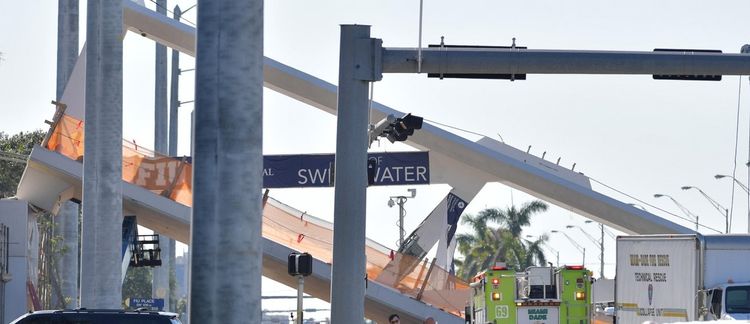
Lesson 1
An uncommon design
A lack of understanding in relation to the bridge's "uncommon" design contributed to the failure in the following ways:
- The bridge’s design and construction were too complex for this kind of procurement. Although the FDOT was an intelligent infrastructure client, FIU was not. FIU administered the project, but had no professional engineers on its payroll. While FDOT did employ professional engineers, it played only a supervisory role.
- National standards did not adequately cover the non-redundant nature of this uncommon single-plane reinforced concrete truss bridge.
“Uncommon design” lessons
TRAINING. Ensure that people know how to identify uncommon designs, the risks they pose and the delivery skills they’ll require.
PROCUREMENT 1. An uncommon design calls for an appraisal of the risks it presents, so that additional costs for the extra management capacity this requires are accounted for, or otherwise the design is rejected.
PROCUREMENT 2. The client was a university, not a seasoned infrastructure client, so it didn’t have professional engineers on the payroll. Given the complexity of the design, the transport authority should have taken more control of the project. Collaborative Reporting for Safer Structures (CROSS) recommends checking how the procurement strategy and contracts align with the competence of those dealing with them and the complexity of the project.
CULTURE. Ensure that people’s enthusiasm for a landmark structure does not obscure the risks presented by an uncommon design.
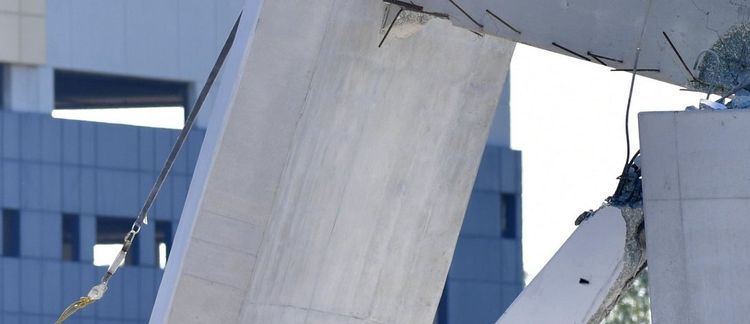
Lesson 2
Structural design errors
Structural design errors contributed to the failure in the following ways:
There were several calculation errors – most notably in node 11/12, which failed.
- The design underestimated loads applied and overestimated capacity, particularly for interface shear demand at critical nodes.
- The design should have considered loadings from all critical construction stages.
- Critical connections such as nodes included voids that reduced the load-bearing capacity of the concrete.
- Drawings did not flag up treatment to prevent discontinuities at nodes, particularly at node 11/12, which reduced its capacity.
Load-path redundancy lessons
TRAINING. Ensure that people know how to identify load-path non-redundant design and manage the risks it poses.
PROCESS/PRACTICE. Cover the concept of load-path redundancy in the design process.
CULTURE. Load-path redundancy is not something that designers alone need to appreciate. Everyone must understand the concept and avoid making decisions that expose the structure to further risks.
REGULATIONS/STANDARDS. These should cover the significance of load-path redundancy in reinforced concrete structures, particularly trusses.
Reinforced concrete lessons
TRAINING 1. Redundancy must be understood and applied correctly to calculations.
TRAINING 2. Detailing reinforced concrete truss structures requires attention to shear resistance at nodal connections.
TRAINING 3. The surface of hardened concrete must be roughened to retain structural continuity across the adjacent concrete pour. This must be indicated on construction drawings.
TRAINING 4. Service ducts in concrete reduce capacity. They should be avoided in critical locations such as nodes, or accounted for as voids in capacity calculations.
REGULATIONS/STANDARDS. Given the large number of basic reinforced concrete detailing errors it has witnessed, the National Transportation Safety Board recommends comparing the design with reasonable estimates for the interface shear demand; the cohesion and friction contributions to interface shear capacity; and the clamping force across the shear surface. (The lack of a precedent for the design in this case should have indicated that the project required a higher level of expertise.)
Works stages/load cases lessons
TRAINING. Teach people to identify different loadings for different stages to determine critical design loads applied.
PROCESS/PRACTICE. For offsite constructions, several stages must be considered in detail (and checked) with the thoroughness of a permanent load case. Stages include partial construction (including back span), formwork removal, transport and tensioning.
CULTURE. The designer and builder need to communicate effectively to ensure that all loading combinations have been identified.
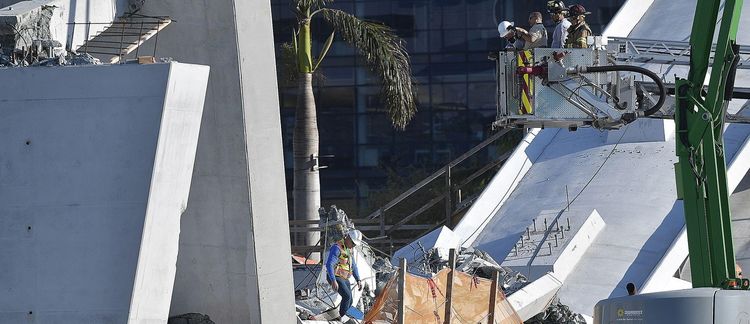
Lesson 3
Structural design errors missed
Problems with the design review process contributed to the failure in the following ways:
- An independent review of the design was a quality-assurance imperative under the state-funded project’s guidelines to provide impartial verification. Insufficient time and funds were assigned to this review. The design-build team initially thought that it could be conducted in-house, but was told that an independent provider qualified to analyse such a complex structure had to do the work. The cost would be borne by the design-build team, which had allocated a budget of $61,000 to the task.
- The designer contracted this work to an independent reviewer without checking whether the FDOT had approved that provider. Instead, it accepted the inclusion of the reviewer’s name in a listing of approved providers on the FDOT’s website as proof. After the collapse, the FDOT stated that there had been an error on its website and that only certificates prove qualification. It had in fact rejected the reviewer’s application to do such work three years earlier. The FDOT didn’t check the firm’s certification either.
The design review was not sufficiently thorough.
- The reviewer’s winning quote of $61,000 was $49,000 lower than the price it had first quoted. It also confirmed that it could complete the work three weeks sooner than it had originally stated.
- The designer assumed that the reviewer would do the same job in seven weeks for $61,000 as it could do in 10 weeks for $110,000.
- After the collapse, the reviewer said that it didn’t check critical nodes or construction-stage load cases because not enough time or money had been allocated to that task.
Lessons about design checks
TRAINING. Ensure that people appreciate the importance of checking designs, especially uncommon ones requiring complex construction techniques, and how to do this using different methods.
PROCUREMENT 1. Allocate enough time and money to checking in accordance with the contract. In this case, the review needed to be as detailed as the original design.
PROCUREMENT 2. Ensure that the scope of checking offered is consistent with the type of structure and its critical areas. In this case, permanent and temporary construction loads needed to be checked, especially as it was an uncommon design and there were risks from working at height over a busy road.
PROCUREMENT 3. A valid certificate is the only proof of qualification. This should still be verified with the certifier.
CULTURE. Suppliers offering by far the cheapest and quickest work will rarely provide the quality of service needed.
Lesson 4
Inadequate response to cracks
Inadequate responses when cracks appeared in the structure contributed to the failure in the following ways:
- Cracks reached unsafe levels yet were not identified as being significant, so they weren’t dealt with appropriately.
- Key choices, such as the decision to re-tension member 11 where the 11/12 node exhibited significant cracking, were not peer reviewed.
- No temporary safety measures were put in place – the road and construction site were not closed – despite the worsening cracks.
Lessons in crack significance
TRAINING 1. All onsite engineers should have ongoing training in how to spot structural faults and report them to their managers for review.
TRAINING 2. Ensure that all responsible parties understand when a fault is becoming a significant risk and what action they should take – for instance, closing the road and shoring up the structure.
TRAINING 3. Adopt technology such as structural health monitoring to aid decision-making where the structure poses a high safety risk.
PROCESS/PRACTICE. CROSS recommends that all increases in crack width, particularly those occurring in a short period, must be taken seriously and assessed by an expert.
CULTURE 1. Factors such as the pressure to deliver on time and the fear of admitting failure can lead people to ignore the warning signs. Construction projects need to create an environment of open reporting where people aren’t inhibited from sharing safety concerns. CROSS exists for this purpose. Concerns should ideally be dealt with on a project as soon as they arise.
CULTURE 2. All parties need to acknowledge that the unthinkable can happen. If there are safety concerns, urgent action must be taken to prevent a disaster – for instance, closing the site and shoring up the structure – followed by a peer review.
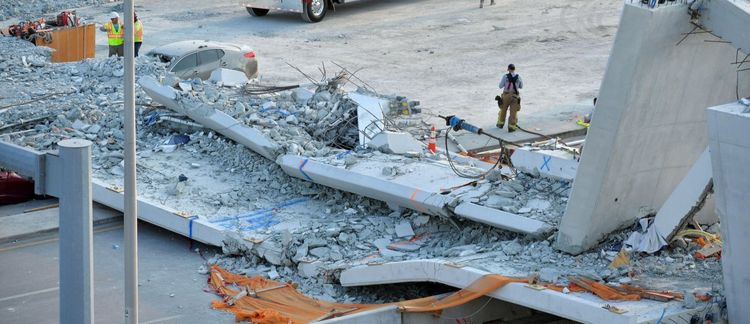
Lesson 5
Engineer of record’s poor judgement
The poor judgement of the engineer of record (EOR) – the professional engineer responsible for preparing, signing, dating, sealing and issuing engineering documents for engineering services – contributed to the failure in the following ways:
- The EOR kept saying the cracks weren’t a problem. Everyone trusted this opinion.
- Working for the designer, the EOR was not independent and may have felt under pressure to uphold the integrity of the design.
- Even when many people raised concerns about the cracks, the EOR’s views weren’t challenged. A peer review is more reliable than one person’s judgement.
EOR’s safety judgement lessons
TRAINING. The EOR is the engineer responsible for the design, who verifies that the structure is being built and operated as required. Responsible engineers onsite must be trained in how to identify signs of structural failure and when to take safety measures such as closing the site, shoring up the structure or ordering a review.
PROCUREMENT. EORs should be independent, so that they’re free to speak out against any party if necessary.
PROCESS/PRACTICE 1. Having a technically qualified design representative onsite is generally good practice as it aids communication between the site and the design office. If this person is not competent and/or independent, the role itself becomes a safety risk. The EOR’s judgement should be reviewed by a suitably experienced multidisciplinary team if there are concerns about it.
PROCESS/PRACTICE 2. The EOR should not alter the construction method without review. Temporary safety measures should be taken during that review.
CULTURE. When there’s a qualified person whose sole responsibility is safety, others can forget that they’re also responsible for it. People should be encouraged to raise any safety concerns, which should be addressed by a diverse multidisciplinary team.
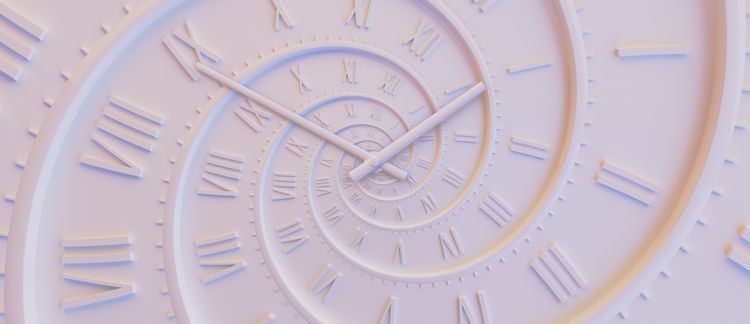
Timeline
How events unfolded
2014 | Jun | FIU receives $11.4m Transport Authority grant to build a bridge over SW Eighth Street. The FDOT will supervise FIU, which lacks in-house engineering expertise. |
---|---|---|
2015 | Sep | FIU receives a proposal for a one-of-a-kind single-plane reinforced concrete truss bridge. |
2016 | Jan | The proposer signs design-build contract with FIU. |
Apr | The designer's failure to consider construction-stage load cases and the non-redundancy of trusses leads to calculation errors and inadequate shear capacity at node 11/12. | |
Jun | The designer learns that its design must be independently reviewed. It would have spent $61,000 doing that review in-house. | |
Jul | A potential reviewer claims to be eligible to check the design but isn’t. Yet it's listed in error on the FDOT website as being qualified, so is considered. | |
Aug | The reviewer slashes its initial quote from $110,000 to $61,000 and pledges to do the job in seven weeks instead of the 10 it first stated. The designer assumes no reduction in scope, but the reviewer will no longer check critical nodes or construction-stage load cases. | |
Sep | The review misses the calculation errors. The casting of the main span on props in a yard beside the road is completed. | |
2018 | Jan-Feb | Tendons and rods are tensioned. |
23 Feb | Prop removal starts. | |
24 Feb | Cracks at node 11/12 are first documented. | |
25 Feb | Prop removal finishes. | |
10 Mar | The span is moved to its final position on the piers across the road. The rods are de-tensioned. | |
10-14 Mar | Further significant cracks are observed, yet no action is taken. | |
15 Mar | The engineer of record enters a meeting in the morning to discuss the cracks, while emergency re-tensioning takes place without being reviewed and the road is left open. At 1.46pm, the bridge collapses, killing six and injuring 10. |